|
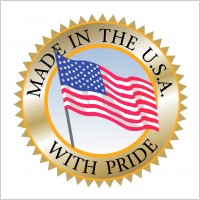
"I could never afford to purchase a Schroeder, and The Woody is every bit as good. Every parameter you could want is easily
adjustable; and it's so damn beautiful, and so musical too." - Ted Danowski
February 13, 2013
For the first entry of this year I've
chosen to copy here a letter to a potential customer who asked about the Woody tonearms, seeking a comparison of the Woody
arms with the SME 3012 arms. This customer also asked about 12 inch and 16 inch arms. Also, once again, I have
explained in the best terms I can why we want an arm/cartridge resonant frequency around 8 Hz.
Greetings Drew, My experience is that the
Woody(tm) tonearms are substantially more musical and more satisfying than the SME 3012 and 3009 arms. The Woody
arms are the most musical arms I have had the pleasure of hearing. When playing a Woody tonearm, with the the Denon
DL103 cartridges I can afford to put at risk, I find myself asking for nothing more. In other words, I am completely
satisfied. This has come to me as a complete surprise after 50 plus years of audio in which I was never fully
satisfied. I have some experience with an SME 3009 (unimproved, i.e. heavy) arm, using a Denon
DL103 cartridge. The effective mass of the 3009 unimproved is better matched to the DL103 than the mass of
the lighter 3009 improved. I don't normally talk about sonics with focus on any particular part
of the sonic spectrum. That said, here goes: With the 3009 unimproved I find the midrange to be quite sweet,
but the bass and treble to be somewhat marginal. The focus is somewhat limited to the midrange, which is
quite nice. With the Denon DL103, my Origin Live (OL1) makes more satisfying music than the 3009 unimproved. This
is with the VTAF on both arms, which greatly improves both the SME and the OL1. Moving forward, the Woody
arms make real music, leaving the 3009 and the OL1 quite far behind. The longest Woody arms I have
made are a substantial number of 12.2 inch (310 mm) arms, and one 14 inch (356 mm) arm. I played a 12.2 inch
Woody and a 14 inch Woody on the same afternoon, both with the same Denon DL103 cartridge. Both made glorious music.
I had the most subtle sense that the 14 inch arm was slightly more refined in sound than the 12 inch arm, but the performance
of the two arms was so lovely and so similar that I'm not certain any perceived difference was not in my imagination.
Both arms were making lovely music. I do have an order now for a 16 inch arm, which will be completed during
this month. It will be interesting to compare the 16 inch arm with the 12 inch arm. I won't have a 14 inch arm in
house to include in this comparison. I love long tonearms. I like the way they handle. And,
I like the fact that anti-skate effects become less significant as the arm becomes longer. Of course, long tonearms
require extra shelf space for their accomodation. But, if one has the space, I recommend a long arm. Also, with
a long arm, there is more wood to look at, which adds to the beauty of the arm. Long Woody arms appear more
slender and refined. I will not be able to strongly recommend a 16 inch Woody until I have heard the one
now on order. I suspect the performance will be excellent. One does not know until one tries. If by
any chance the first 16 inch arm is found less desirable than a 14 inch arm, it will be reworked to the 14 inch length. I design and manufacture Woody tonearms to meet the cartridge needs of the owner. In particular, I design
for an arm/cartridge resonant frequency around 8 Hz. The physics and mathematics of the situation dictate that the vibrational
amplitude (undesired) of the headshell in response to stylus forces is proportional to the arm/cartridge resonant frequency.
This holds true across the entire audio spectrum. Thus, one wants the lowest practical arm/cartridge resonant frequency.
Below 8 Hz the risk of problems from warp and footfall increases, so we shoot for 8 Hz. I look forward to
discussing your tonearm needs at greater length. Kind Regards, Pete
February 13, 2013
Phono Stage Comparison:
Last night I had old friend Bill Van Winkle
over. We listened to the State of the Union Address, had dinner and an ice cream cone, and then retired to the Garden
of Earthly Delights with our wine glasses. Bill is a retired piano tuner, blind from an early age. Despite advancing
years, his hearing remains robust. Needless to say, Bill has listening skills.
We played excerpts from the
same several records through two different phono stages.
The first of these phono stages is the Kara Chaffee
Model 222, which is a combined tube phono stage and tape playback stage, using a single op amp at the input of each channel
to get something like 10 or 15 dB of low noise gain before handing the signal to 12AX7 vacuum tubes. In this unit we
like the EI 12AX7. The EI 12AX7 tubes are NOS units from the Serbian plant that was bombed out during the Kosovo
nightmare. The 222 was originally designed as a tape playback stage. I purchased the 222 because of its lovely
soncis in tape playback. I've never heard tape sound so wonderful. It made sense that because this is a fabulous tape
stage, it could could also be a fabulous phono stage. When I had begged sufficiently, Kara added phono EQ
to the unit for me. The phono performance equals the tape performance.
This is the best phono stage I've had the privilege of having in my system.
Good news now. After long consideration, Kara is
now offering the Model 222 as a combined phono and tape stage, priced around $2500, if I am not mistaken. In my analysis,
this comes down to $1250 for the best phono stage I've heard, and $1250 for the best tape stage I've heard.
The second phono stage we played last night is a modified Jolida JD9. The modifications
include better 12AX7 tubes (the EI units), replacement of three of the op amps in each channel with improved op amps,
replacement of the coupling caps with specific Obligatto brand caps from Brian Cherry, and damping of the chassis with self
adhesive damping material.
Cutting to the chase, the Chaffee Model 222 substantially outperformed the
Jolida JD9. With the Model 222, Massed strings were more transparent and lovely; the music had more body; the sense
of space was superior; and, in summary, the music was more musical.
April 12, 2013 Experience with Permalloy Output
Transformers
My wing man Stephaen Harrell and I recently have had an interesting experience with Permalloy
(nickel alloy) output transformers in George Wright series configured single ended 2A3 amplifiers used only for the midrange
of our horn systems.
Mike LaFevre of Magnaquest, hearing of our enthusiasm for nickel output transformers
says we really ought to try parallel feed 2A3 amps in our midrange. These amps work nicely with small nickel output
transformers. Maybe we need to start hanging around the Bottlehead folks.
Here is a summary:
Some time a few years ago,
George Wright purchased a pair of air gapped nickel transformers from Mike LaFevre and put them on a pair of his
single ended 2A3 amps. Fast forward. My wing man, Stephaen Harrell purchased these amps from original owner about
a month ago, not fully realizing what he was getting. Stephaen and I have very similar all horn systems.
No metal diaphragms. RCA 9584A theater drivers on midrange. Multi-amped. Steep crossovers at 350 and 6k.
At Stephaen's we installed these amps in place of another pair of Wright single ended 2A3 and
began to play music. I sat quietly for about 15 minutes, before I said to Stephaen. Is it just me, or is something
special happening here. Stephaen replied something like "Oh yeah!" Stephaen did some digging and
found out these transformers, not painted black, nickel looking lams, are air gapped nickel made by Mile LaFevre of Magnequest.
Mike says he has made only 3 or 4 pair of these.
Played the amps in my system.
Once again, "Yes Baby!" Have listened extensively since. Still "Yes Baby." Loads of
inner detail, layering, and space, but very mellow and seductive. Nothing clinical at all.
OK. So I have to have a pair of these transformers for my Wright 2A3 amps. I contact Mike LaFevre.
Has limited supply of the nickel EI lams. Not sure he wants to do it.
So I google permalam
etc. and get very few leads. Trying to figure
out if we are nuts. So I begin modeling what is going on, in my crude way. My doodling indicates some reduction
of inductance, but it is a long way from 35 Hz to 350 Hz. Should be good at 350 Hz. Also some loss of power handling.
But the transformer is an 8 watt nominal device with silicon steel. Saturation flux with nickel is about 2/3 of saturation
flux with silicon steel. This limits flux swing and primary current to maybe 2/3 of silicon steel flux swing, and power
handling to maybe 4/9 of silicon steel power handling. 4/9 of 8 watts is about 3 watts. 2A3 isn't good
for much more. And then, how much music power is there above 350 Hz? And we have 105 dB/watt horns.
In the mean time Mike gets inspired by the enthusiasm oozing from myself and Stephaen,
and steps up to the plate. Says he will do it if we give him some time. Says this will use up the last of his
nickel lams in this size, which makes him sad. Made half payment this week.
Some time a few years ago, George Wright purchased a pair of air gapped nickel transformers from Mike LaFevre
and put them on a pair of his single ended 2A3 amps. Fast forward. My wing man, Stephaen Harrell purchased
these amps from original owner about a month ago, not fully realizing what he was getting. Stephaen
and I have very similar all horn systems. No metal diaphragms. RCA 9584A theater drivers on midrange. Multi-amped.
Steep crossovers at 350 and 6k.
At Stephaen's we installed these amps in place of another pair
of Wright single ended 2A3 and began to play music. I sat quietly for about 15 minutes, before I said to Stephaen.
Is it just me, or is something special happening here. Stephaen replied something like "Oh yeah!"
Stephaen did some digging and found out these transformers, not painted black, nickel looking lams, are air gapped nickel
made by Mile LaFevre of Magnequest. Mike says he has made only 3 or 4 pair of these.
Played the amps in my system. Once again, "Yes Baby!" Have listened extensively since.
Still "Yes Baby." Loads of inner detail, layering, and space, but very mellow and seductive. Nothing
clinical at all.
OK. So I have to have a pair of these transformers for my
Wright 2A3 amps. I contact Mike LaFevre. Has limited supply of the nickel EI lams. Not sure he wants to
do it.
So I google permalam etc. and get very few leads. Trying to figure out if we are nuts. So I begin modeling what is going on, in my crude way. My
doodling indicates some reduction of inductance, but it is a long way from 35 Hz to 350 Hz. Should be good at 350 Hz.
Also some loss of power handling. But the transformer is an 8 watt nominal device with silicon steel. Saturation
flux with nickel is about 2/3 of saturation flux with silicon steel. This limits flux swing and primary current to maybe
2/3 of silicon steel flux swing, and power handling to maybe 4/9 of silicon steel power handling. 4/9 of 8 watts
is about 3 watts. 2A3 isn't good for much more. And then, how much music power is there above 350 Hz? And
we have 105 dB/watt horns.
In the mean time Mike gets inspired by the
enthusiasm oozing from myself and Stephaen, and steps up to the plate. Says he will do it if we give him some time.
Says this will use up the last of his nickel lams in this size, which makes him sad. Made half payment this week.
|